WELCOME TO SLEMON PARK (HANGAR 8)
Team Energy Aero: Innovating Towards the Future


PROJECT SUMMARY
A feasibility study to be conducted on Hangar 8, a 300,000 sq. foot facility, to evaluate the heating and energy management system currently in place and make recommendations improve the overall efficiency of the heating operation to reduce the heating expenses.
Recommendations:
Replacing Oiler Boilers with Biomass Boiler
Automated Controls System With Temperature Setback
Spray Foam Insulation
Radiant Tube Heaters
Air Curtains
​
Impact of Recommendations:
Potential Annual Savings over $170,000
Annual Emissions Reduced By 98%
Air Curtain reduces heat recovery time by 28%
Temperature Setback Saves 15% fuel consumption alone
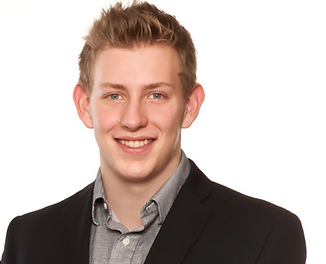
DYLAN MACISAAC
Project Manager
4th year Mechatronics
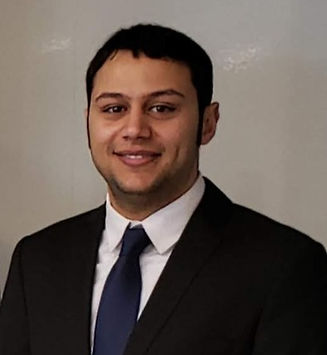
HASSAN ALMALKI
Sustainable Design
4th year Sustainable Energy

MYRIAM GEORGES
Sustainable Design
4th year Bio-resources
BACKGROUND INFORMATION
Slemon Park Corporation
Slemon Park Corporation is a property management company which owns an operates a business community both on the residential and commercial side. The facility was originally built as a military base in the late 1950s to early 1960s; Slemon Park Corporation took over operations in 1992. Out of the multiple properties within Slemon Park, the team focused on Hangar 8 a 300,000 sq. foot facility.
The Problem
Slemon Park Corporation currently has an ageing and oversized heating system from a retrofit from when the property was converted from an air base to privately owned commercially leased buildings. The currently heating system is reliant upon the 500hp boiler that produces steam to meet all the heating demands in the facility. The steam is used directly in heat distribution systems, as well as, being run into two heat exchangers to supply multiple hot water loops that are also run in the building. The system is run primarily by pneumatic control systems or by the power engineer on duty adjust valves manually resulting in poor response times. The major fuel source for the building in # 6 fuel oil that is increasing unreliable to procure as well as having a large environmental impact. The need to find more sustainable fuel source and heating methods to meet the heating loads of Hangar 8 is required as well as find methods to reduce the annual heating expenses of Slemon Park Corporation.
THE PROCESS
Calculations & Testing
THERMAL IMAGING
Thermal Imaging testing was conducted at Hangar 8 on the Hangar doors as Slemon Park indicated that they were having difficulty regulating the temperature in the large hangar space. Using a thermal imaging camera the team took over 100 thermal images of the hangar doors over different days and weather conditions. The results all lead to the same conclusion of large heat transfer losses especially around the gaps between the doors and along the bottom of the doors. This lead to the recommendations of the insulation discussed in the recommendation section.
![]() Thermal Image Plot of Hangar Door Day 1MATLAB Plot of Thermal Imager Data | ![]() Thermal Image Plot of Hangar Door Day 2MATLAB Plot of Thermal Imager Data |
---|
RADIANT VS. FAN COIL HEATING
Testing was conducted to show that radiant heating is a more practical method of heating large volume rooms such as a hangar or warehouse. This is because with traditional air heating system the heat rises and more energy has to be used to ensure the area occupied by people is kept at a comfortable temperature. Radiant heating works by heating physical objects that s within the coverage of the heater, allowing for reduced energy demand as well as achiving the desired temperature much faster.
RETSCREEN
RETScreen is an industry standard software used to evaluate the feasibility by green energy projects. The software was used to show the possible savings of energy, fuel consumption, financially as well as emissions rates. A study was conducted using the equipment that finical estimations had been received for being, the biomass boiler, spray foam insulation, and controls equipment with temperature setback. The results were that Slemon Park Corporation potentially could save over $170,000 annually, with 19.5% reduction in required fuel consumption and 16% in overall energy demand and a 98% reduction in tCO2eq emissions.
![]() Emissions SavingsGreen area is removed emissions | ![]() Equivalent Emissions Reduction | ![]() Natural Recourse Canada Data on Emissions |
---|---|---|
![]() Payback Period for Pre-Tax cost | ![]() Finical Model for 20 years |
THERMAL LOADING CALCULATIONS
To ensure that the boiler and additional heating equipment is sized correctly the thermal load of the building was calculated. To determine the size of heating equipment required the known energy used along with the efficiencies of the current heating equipment was used to determine the amount of energy required to heat the building during the coldest months of the year. The energy data was then normalized using weather data over the past 30 years and following the ASHRAE design standards of 99.6% design temperature and a safety factor of 1.4. The results of the analysis showed that the boiler size could be greatly reduced from the current 6.4MW boiler to a 2.4MW system.
![]() Thermal Loss Overview | ![]() Thermal Loading CalculationsTo ensure the building can maintain the design temperature the amount of thermal energy required to overcome the thermal loss of the building |
---|
RECOMMENDATIONS
What We’ve Accomplished
ACKNOWLEDGEMENTS
Thank You To Our Client & Contacts at UPEI

SLEMON PARK CORPORATION
Industry Partner
David Anderson
Power Engineers:
Joey & Stephen
​

UNIVERSITY OF PRINCE EDWARD ISLAND
Faculty of Sustainable Design Engineering
Dr. Grant McSorley
Dr. Ali Ahmadi
Dave TaylorÂ
Chuck Terrio
Anthony Van Beek
Tyler Gallant Â
Holly Barret
Industry Partnership
CONTACT US FOR MORE INFORMATION
For More Information Or Any Questions Feel Free To Contact
(902) 439-2472 || (902) 579-3584